It Was, It Still Is, But Will It Always Be ‘the Dirty Connector’….?
One of the many hopes for network operators who deploy optical fiber has been, of course, its performance & reliability. Most if not all hope that the general maintenance requirement will be greatly reduced with the use of fiber optics as compared to conventional copper as optics does not rust, does not get affected by electromagnectic inteference and is water resistant. Nevertheless, many network operators around the world realize that the optical network does not always perform as it should and to their horror, it is the simplest of components in the network which, more often than not, are the culprits of their network failures. That component is none other than the optical connector, dubbed the ‘weakest link’ of the network. Based on a study conducted by NTT Advanced Technology, 4 of the top 5 causes of network faults are connector related and the No.1 cause is contaminated connector end faces. The same problem is reported by major optical fiber network operators around the world with the lack of appreciation for fiber cleanliness accounting for 90% of all reported faults.
In the past, connector contamination in optical transport networks or data center fiber interconnect networks were less prevalent due to the lower transmission speed and most of the optics were located in controlled environments of exchanges or data centers and are deployed and maintained by highly trained professionals. However, with the increasing deployment of optical fiber outside plant networks, optical connectors are widely used in outdoor enclosures such as roadside cabinets and pedestals as well as in customer premises whereby dust & humidity are uncontrolled. Lets imagine the core of a single mode connector is only 9μm and if a piece of dirt, speck of dust or oil smudge in the right position will cause high reflection, insertion loss and potential fiber damage. Connector cleanliness is even more critical in high power transmission systems such as DWDM systems or long haul transmission where Raman amplifiers are used, the optical signal transmission power may be 1W to 5W. In a single mode fiber transmission, such high power transmission may burn the contaminant and fuse the dirt with the silica material of the optical fiber, thus requiring the replacement of the connector. The source of contamination is usually due to connector mishandling and a lack of understanding for optical cleanliness.
You may be surprised that some of the most common causes for contaminating optical connectors are nothing more than carelessness such as:
- Leaving a connector uncapped for even a short period of time where it will be exposed to dust contamination.
- Touching the connector end face with fingers thus leaving skin oil or passing on dirt.
- Using unsuitable cleaning methods or products such as tissue, water or even shirt sleeves.
- Assuming that connectors which are protected by dust caps are clean or factory guarantee cleaned.
- Not cleaning both connector end faces before making a connection.
Luckily, there are optical cleaning tools that are specialized to remove contaminants from optical connectors and bulkheads. The standard document, ‘IEC 62627-01: Fibre optic interconnecting devices and passive components – Technical Report – Part 01: Fibre optic connector cleaning methods’ actually describes a comprehensive cleaning methodology and is usually adopted as the industry’s best practice. Nevertheless, the accelerated adoption of multifiber connectors such as the MPO connector in data centers, has posed a even higher degrees of challenges to maintaining the connector cleanliness. Unlike single fiber connectors, the cleanliness of the total surface of a multi-fiber connector such as the MPO connector is also critical to making a proper connection. The array of fibers is presented on a flat surface which comes into full contact when terminated. Any contaminant around the optical fibers and alignment pin prevents will full contact of the two connectors thus creating an air space which reduces the connector performance in term of both the Insertion Loss and Return Loss. Unfortunately, conventional MPO cleaning tools such as the pen cleaner ONLY clears contaminants around the optical fiber array but however the space around the alignment pins remains contaminated.
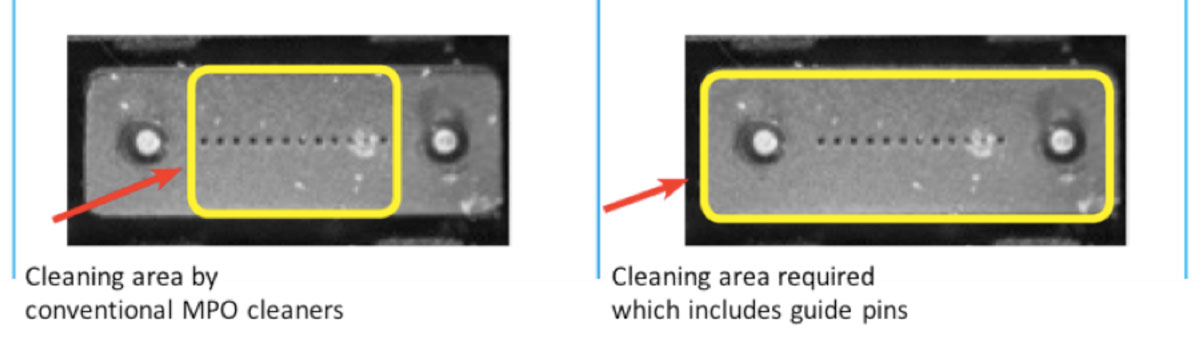
Table 1 – ASHRAE Guideline
Fortunately, there are cleaning tools that are capable of cleaning the whole endface of the MPO, including the guide pin and by using this new type of MPO cleaning tool, one is able to effectively remove oil, dust and dirt particulate from the ENTIRE connector endface.